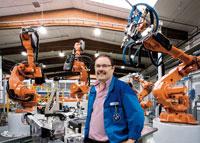
Zuverlässige Energiezuführung von Roboterwerkzeugen für die Türen des BMW X1
Nur 57 Sekunden benötigen die Industrieroboter, um eine Tür für den neuen BMW X1 zu bauen. Leisten sollen sie das möglichst sieben Jahre lang – und zwar schadenfrei. Das ist Schwerstarbeit auch für die Energiezuführungssysteme der Roboterwerkzeuge von Robotec Systems. Sämtliche Herausforderungen bei dieser Anwendung wie die erstmalige Lastdatenermittlung hat die HELUKABEL-Tochter mit Bravour gemeistert.
Nahe Regensburg im bayerischen Elsendorf entsteht derzeit eine hochmoderne Anlage zur Fertigung der Türen für den neuen BMW X1. „Wir von BMW übernehmen anfangs die Regie. Als Dienstleister planen wir die Anlage, wählen die Lieferanten aus und bauen die Anlage komplett auf. Wenn alles läuft, übergeben wir sie an den Eigentümer – unseren Zulieferer Magna“, berichtet Manfred Scheuerer, der bei BMW für die Fertigungsplanung verantwortlich ist und ergänzt: „Über dieses sogenannte Drittkundengeschäft setzen wir weltweit Produktions- und Qualitätsstandards.“
Wie im Automobilbau üblich, übernehmen auch in der Türenproduktion Roboter weitestgehend die Arbeit. 76 Großserienroboter stehen in der riesigen Halle. Sie sind aufgeteilt auf vier Anlagen zur Produktion der zwei Vorder- und Rücktüren. Hier werden im Dreischichtbetrieb rund 700.000 Türen im Jahr aus den von Magna in Graz gefertigten Blechteilen mit Punktschweißzange und Klebepistole zusammengebaut.
Eine Million Torsionszyklen
Sieben Jahre lang soll die Anlage möglichst störungsfrei laufen. Da Roboter prinzipiell ohne Werkzeug angeboten werden, benötigen sie ein Versorgungssystem: Strom, Kühlwasser, Daten und Klebemittel müssen via Kabel oder Schlauch an den Werkzeugkopf geführt werden. Neben den standardisierten technischen Spezifikationen der Kabel und Schläuche für die jeweiligen Werkzeuge definiert BMW auch qualitative Anforderungen. Diese sind als Formel im Lastenheft hinterlegt und berechnen sich aus der maximal tolerierten Stillstandszeit der Anlage.Volker Elbe, Vertriebsleiter bei Robotec Systems, erklärt: „Die Belastung der Kabel- und Schlauchpakete ist zum einen von den Bewegungsradien der Roboterarme abhängig. Zum anderen lässt es sich bei Schweißrobotern nicht verhindern, dass der Abbrand zwischen Kabel und Schläuche gelangt und dort bei allen Bewegungen wie Schmirgelpapier wirkt. Das erhöht den Verschleiß zusätzlich und kann die Lebenszeit verkürzen. Doch in unserer internen Qualitätskontrolle müssen alle Produkte eine Million Torsionszyklen überstehen. Möglich wird das erst durch die Konstruktion und Materialzusammensetzung der verwendeten Kabel von HELUKABEL. So stellen wir sicher, dass unsere Systeme auch den hohen Anforderungen von BMW standhalten.“
Robotec Systems hat sich auf die Adaption von Kabeln, Leitungen und Schläuchen zur Versorgung von Applikationswerkzeugen an Industrierobotern spezialisiert. Die Automotive-Branche von OEM bis Tier 1 schätzt die Symbiose aus Kabelwerk und Engineering-Know-how.
Simulation schafft Klarheit
In der Produktionsplanung gilt es grundsätzlich, Überkapazitäten zu vermeiden. Anlagengröße und-design werden deshalb mit Produktionsplanungssoftware vorab simuliert. „Ausgehend von der Jahresproduktion und der Taktzeit berechnen wir die Leistungsdaten für jeden einzelnen Roboter. Dazu benötigen wir Simulationsdaten für alle Teile, die der Roboter bewegen muss. Nur so können wir die Roboterleistung exakt auf die tatsächlichen Erfordernisse auslegen“, erklärt Manfred Scheuerer und ergänzt: „Die Last addiert sich aus allen Teilen, die der Roboter in der vorgegebenen Taktzeit bewegen muss. Dazu zählt neben den Werkzeugen, dem Handling und natürlich dem Werkstück selbst auch das Energiezuführungssystem für die Werkzeuge.“
Dieses besteht aus zwei Komponenten: Zum sogenannten „Support“ zählen erstens die Teile, welche die Schnittstelle zu den jeweiligen Industrierobotern bilden. Vorzugsweise bestehen diese Komponenten aus Metall und Kunststoff. Wichtigste Baugruppe des Supports ist das Rückführsystem, welches ein enges Anliegen der zweiten Komponente „Energiepaket“ an den Roboter garantiert. Dadurch werden unkontrollierte Störkonturen verhindert, die zum Crash oder Stillstand einer Fertigungsanlage führen können. Das Energiepaket besteht aus einem sehr leistungsfähigen Wellrohr mit etwa 70 Millimeter Durchmesser. In dem Rohr befinden sich die konfektionierten Kabel, Leitungen und Schläuche.
Die Simulationsdaten basieren unter anderem auf den CAD-Daten der Konstruktion und einem kinematisierten Robotermodell. Sie geben Auskunft über Gewichtsdaten und die exakte Lage des Schwerpunkts. Schließlich offerieren sie ein exaktes Abbild des kompletten Systems, bestehend aus Support und Energiepaket. „Unser Ziel ist es, alle Roboter auf 90 Prozent Auslastung auszulegen. Dann sind wir mit Blick auf die Laufzeit der Anlage von sieben Jahren auf der sicheren Seite“, meint der BMW-Planer.
Erstmals Lastdaten ermittelt
„Eine der Herausforderungen im Rahmen des Projekts war es, die geforderten Lastdaten für BMW bereitzustellen“, berichtet Volker Elbe. „Das Stichwort heißt ‚biegeschlaffe Elemente‘. Keinem war es bislang gelungen, das exakte Verhalten eines Seiles zu simulieren. Ebenso chaotisch verhält sich auch ein Energiepaket. Aus einem Mix aus Engineering am CAD und empirischen Versuchen gelang es uns, den Schwerpunkt der Masse zu ermitteln und wie sich das Gewicht während der Bewegung des Roboters verhält und verteilt.“Immerhin kommen mit Kabeln und Schläuchen, die wie ein Rucksack auf dem Roboterarm sitzen, über 40 Kilogramm Marschgepäck zusammen. Dieses setzt sich aus den Komponenten ‚Support‘ und ‚Energiepaket‘ zusammen, die für das Punktschweißen und das Handling benötigt werden.
Der Roboter ist in zwei Achsbereiche unterteilt: Die Achsen eins bis drei verhalten sich recht statisch und die Achsen drei bis sechs sehr dynamisch. Für letztere Achsen geben die Lastdaten Auskunft über die Performance des Roboters. Mit ihnen lässt sich ermitteln, wie schnell sich seine Achsen bewegen und welche Last sie tragen können.
Medien aller Art
Die Energiepakete für die Anwendungen Handling und Punktschweißen bestehen oftmals aus 25 bis 35 mm² Primärkabeln wie mehradrige Steuerkabel, Motor-und Resolverkabel, Datenkabel beispielsweise für Profinet, Kupferkabel, Lichtwellenleiter, Erdungsleitungen und Schläuche für die Versorgung des Werkzeugs.Darüber hinaus gibt es aber noch jegliche erdenkliche andere Art von Medien wie Hydraulikleitungen, spezielle Hybridkabel oder Verbrauchsmedien wie Nieten oder Schweißbolzen. „In diesen Kabeln, Leitungen und Schläuchen steckt viel Know-how. Schließlich konnte sich Robotec Systems über ein Ausschreibungsverfahren bei BMW als Lieferant etablieren und mehr noch: „Dank dieses Projektes können wir heute für alle unsere Systeme Last- und 3D-Simulationsdaten bereitstellen. Wir haben unsere Erfahrungen auf diesem Gebiet ausgebaut, sodass auch künftige Kunden davon profitieren“, freut sich Volker Elbe.
Im Herbst 2013 hatte BMW die ersten 30 Systeme für Handling-, Klebe- und Punktschweißroboter bestellt. Robotec Systems lieferte und montierte sie bereits etwa sechs Wochen später. Mittlerweile sind alle Roboter bestückt und BMW-Planer Manfred Scheuerer hat die Anlage an Magna übergeben.
Hannover Messe Halle 13, Stand C98
Bilder:
Bild oben: Manfred Scheuerer, BMW: Wir haben die Werkzeugköpfe der Roboter mit Energiezuführungssystemen von Robotec Systems ausgerüstet. Für uns ist es wichtig, dass diese in der Anlage sieben Jahre lang störungsfrei laufen.
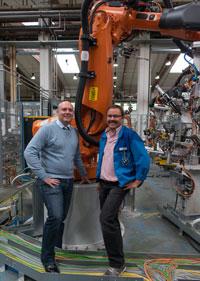
Volker Elbe, Robotec Systems (l.) und Manfred Scheuerer, BMW (r.): Die größte Herausforderung bei diesem Projekt hat Robotec Systems mit der Erstellung der Lastdaten gemeistert.
Download: Text Bilder
Kontakt:
HELUKABEL GmbH
Dieselstraße8-12
71282 Hemmingen
Tel.: 07150/9209 339, Fax: 07150/9209 5339
E-Mail: Diese E-Mail-Adresse ist vor Spambots geschützt! Zur Anzeige muss JavaScript eingeschaltet sein!, Web: http://www.helukabel.de
Bei Veröffentlichung erbitten wir je ein Belegexemplar.
Pressebüro: Presse Service Büro GbR, Strogenstraße 16, 85465 Langenpreising, Tel.: 0171/714 2316